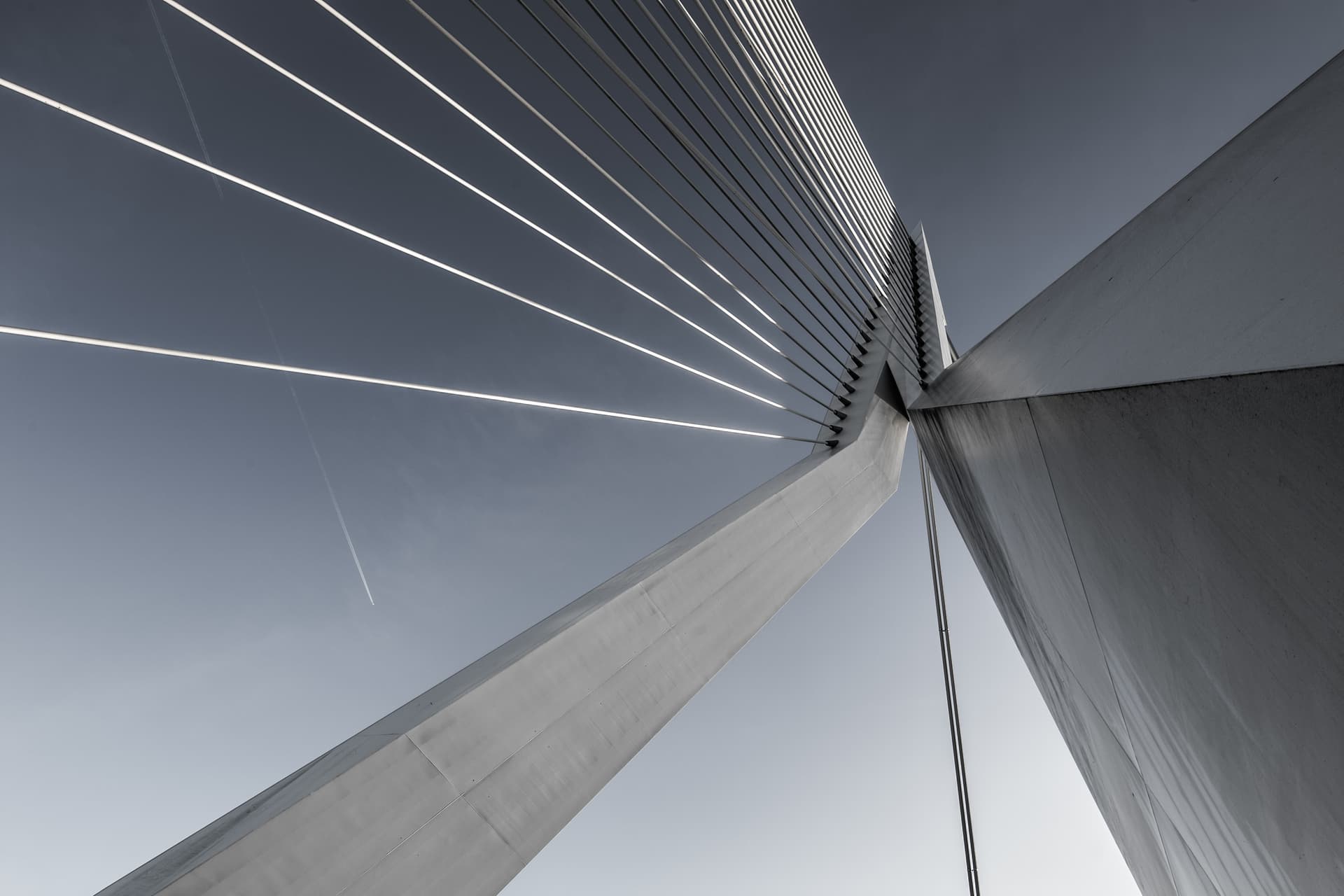
About
COCOONCO2 is committed to providing innovative carbon management solutions for the construction industry. By leveraging advanced technologies and expertise, we help cement, concrete, and building industries achieve net-zero carbon emissions by 2050.
Vision and Mission
Vision
To lead the construction industry toward sustainability with innovative carbon reduction and carbon sink technologies.
Mission
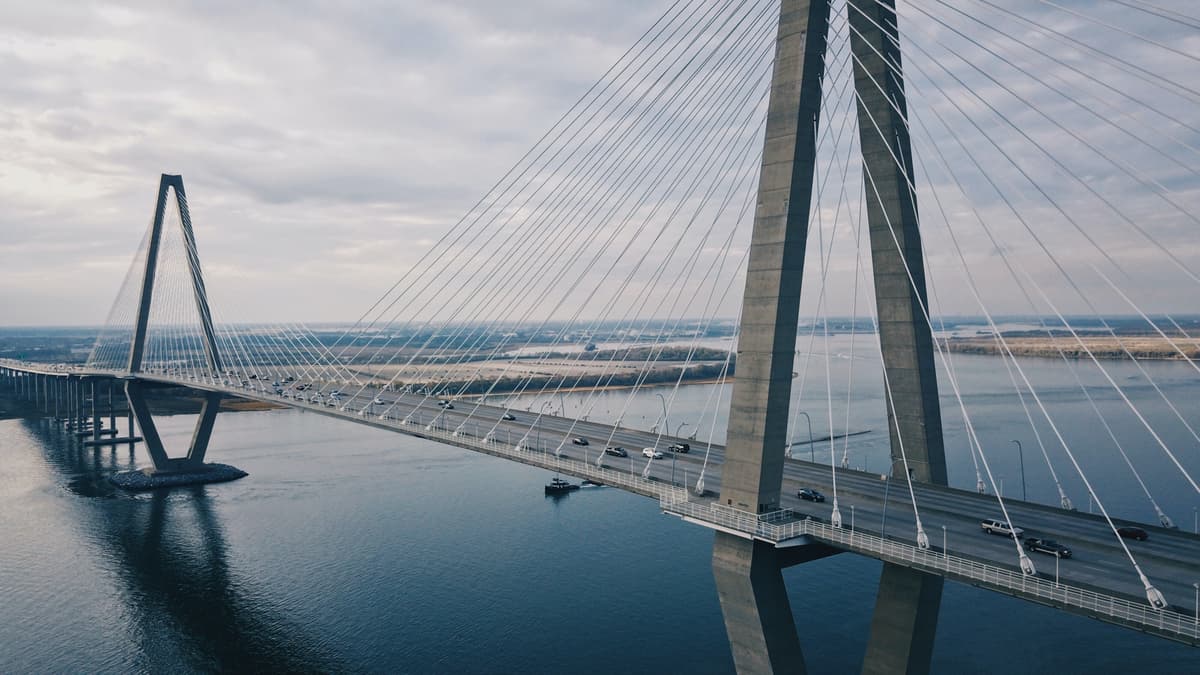
1. Enable cost savings in raw materials and improve production efficiency.
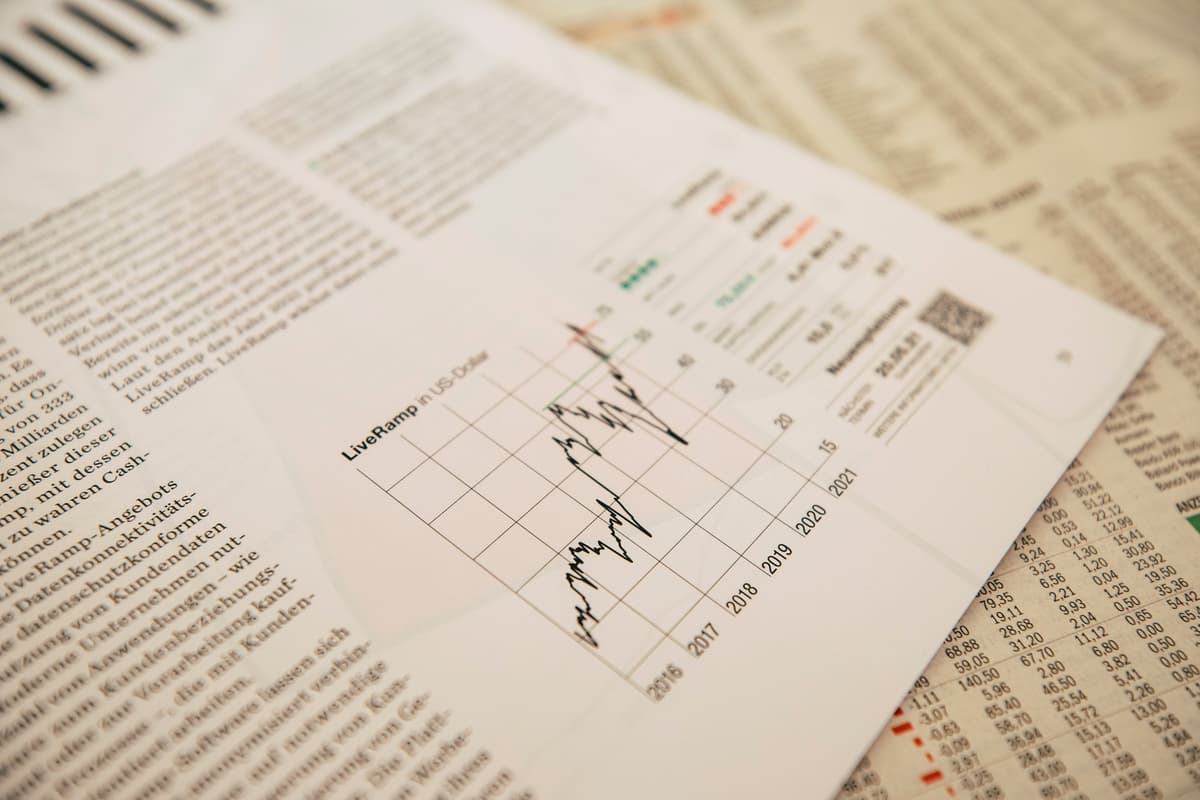
2. Reduce environmental protection costs through recycling.
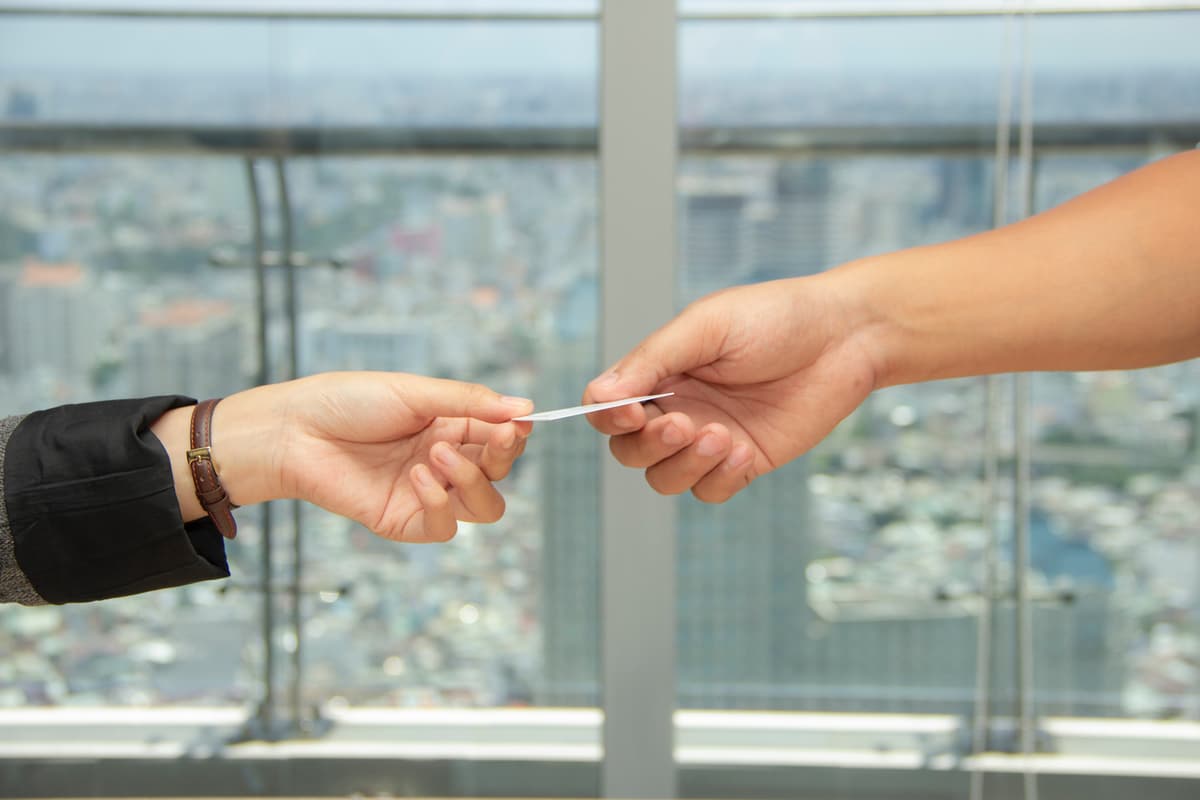
3. Offer technical solutions to mitigate carbon tax impacts by reducing carbon emission, generating carbon credits and certifying low-carbon footprint products.
Background
The construction industry is a massive contributor to global carbon emissions. Cement production alone generates 0.8~ 1.0 kg of CO₂ per kg of cement, primarily due to chemical reactions and energy use. Through innovative technologies, emissions can be reduced to as low as 0.7 kg per kg by replacing clinker and adopting low-carbon alternatives. Then extending to downstream applications, furthermore, the closed-loop design to significantly reduce carbon emission from cement and concrete’s manufacturing to buildings’ life cycle assessment.
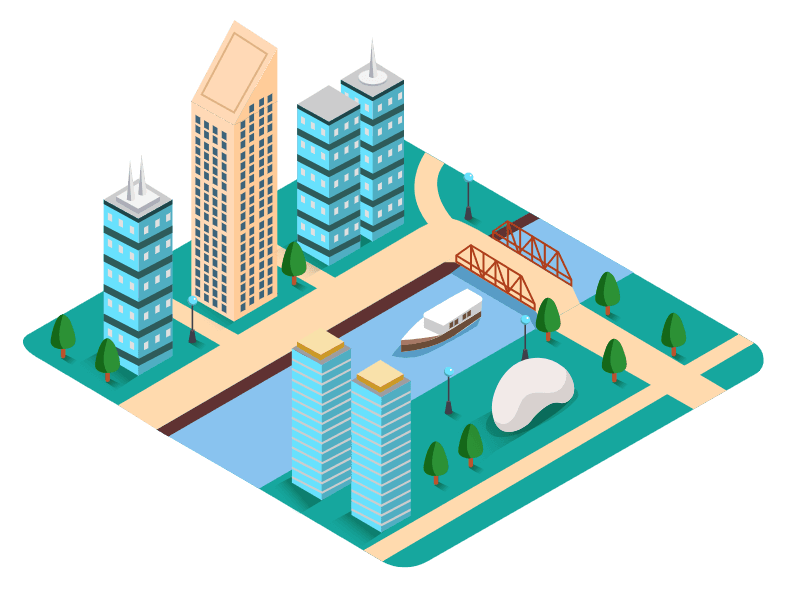
Technologies
COCOONCO2 employs three core technologies to reduce carbon emissions effectively:
1. Grinding Aids (GA)
Enhances the compression strength and grinding efficiency in cement and limestone grinding processing.
2. Carbon Abating Agent (CAA)
Embeds CO₂ into cement as a permanent carbon sink via CCS/CCU.
3. Reclaiming Water Solution (RWS)
Recycles wash-water from concrete transportation, turning it into useful fillers into fresh concrete. Mineralizes recycled solid wastes as applicable construction materials.
Applications
COCOONCO2 solutions can be applied to the following areas:
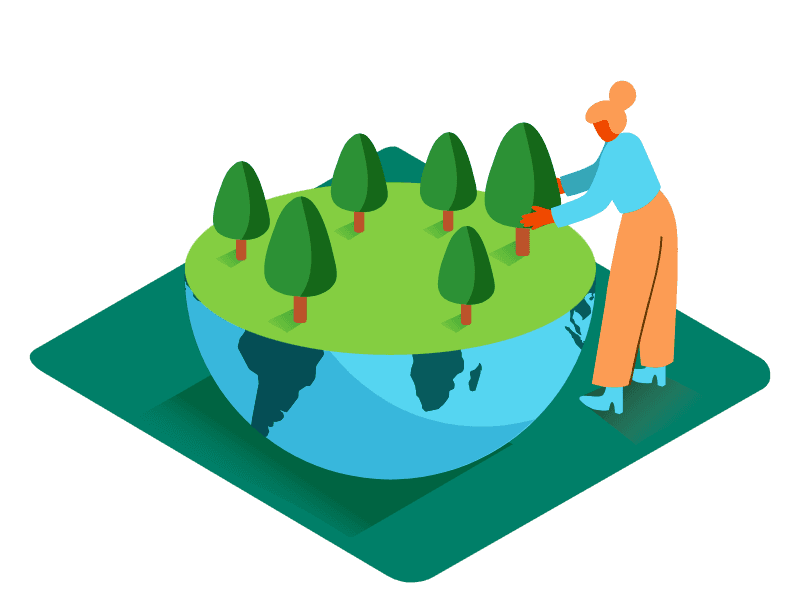
Certifications
COCOONCO2 technologies support carbon footprint verification, including:
1. SGS and BSI strength certifications
2. Carbon storage analysis from sequestered CO₂ via carbon & sulfur analyzer
3. SEM imaging for structural analysis
Carbon Management Platform
The platform helps customers register for Verified Carbon Standard (VCS) and obtain Verified Carbon Units (VCU) to respective local authorities or international carbon management organizations (such as Verra and Golden Standard), provides methodologies with defined boundary conditions, so as to acquire low carbon footprint certificate and/or carbon credit. It also assists in tracking and managing carbon reductions measurement to optimize cost savings in raw materials and carbon impacts.
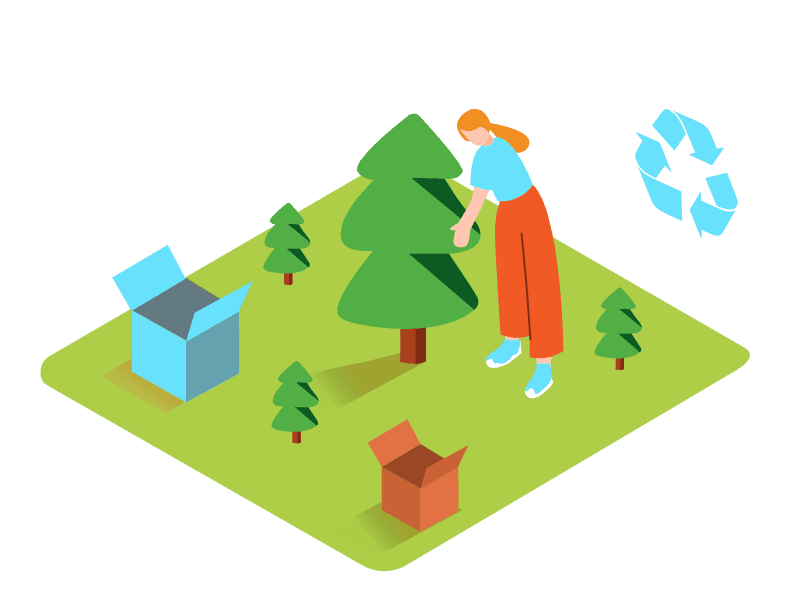
It’s to provide the service to COCOONCO2 clients working together for a verified option VCS with VCU, as a proof of a lowered and recognized PCF, as well as transaction of carbon rights in public platforms.
Verified Carbon System
Under construction.
Verified Carbon Unit
Under construction.
Customer registration and login
Please click to download the form